Flexographic printing may sound like a technical marvel reserved for the elite, but in reality, it’s a game-changing innovation that’s been quietly revolutionizing industries for years. Often overshadowed by its mystique, flexo printing stands as an affordable and versatile solution used extensively in label and food package printing, for decades. But there’s more to it than meets the eye.
Let’s unravel the intricacies, advantages, and applications of flexographic printing—a sustainable choice for modern printing needs.
Table of Contents
What is Flexographic Printing?
Flexographic printing is not a new-gen technology. It has been used everywhere for ages but has evolved today in surprising ways. There’s practically nothing that can’t be produced through flexography. From snack bags, chocolate wrappers, shampoo bottles, self-adhesive labels, cereal boxes, notebooks, pizza boxes, desk calendars, and printed paper towels, there’s no area untouched by flexo printing.
Derived from rubber stamp printing, which was popular in the early 1900s, flexography replaced the inks used in rubber stamp printing—proven unsafe for food packaging—with flexible photopolymer printing plates. These plates have the capability to transfer ink to nearly any substrate, including metal, plastic, corrugated cardboard, paper, and even non-woven fabric.
Commonly used for high-volume label and flexible packaging printing, flexo printing is a high-speed, roll-feed web printing process, renowned for its unparalleled speed. Its capability to achieve up to 2000 linear feet per minute showcases the remarkable speed and efficiency of this printing method.
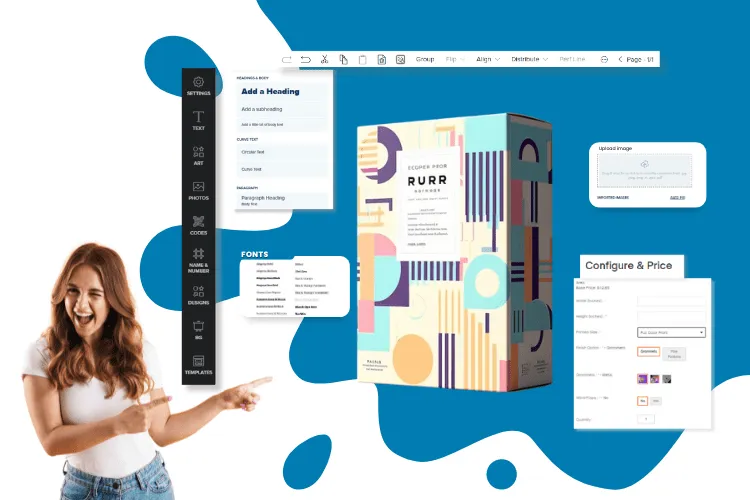
Get 5x More Clients
Elevate your business growth
by integrating DesignNBuy
into your workflow.
The Flexo-Printing Process: How It Works
Flexographic printing progresses through three distinct stages: Pre-press, Printing, and Post-press. Now, let’s explore each stage meticulously.
1. Pre-press stage in flexographic printing:
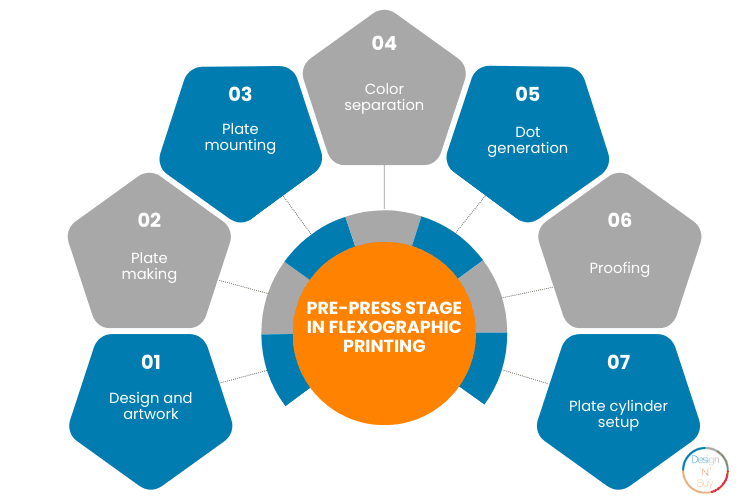
Design and artwork
The first step of preparing for flexographic printing is to create a design or artwork that needs to be printed, using online graphic design software. It should be prepared with consideration for the flexographic printing process, taking into account factors like color separation, trapping, and the use of line screens.
Plate making
The designed image is transferred to a flexographic printing plate, typically done by creating a film negative of the design. The printing plate is usually made of a flexible material, often photopolymer, which is sensitive to UV light. The plate-making process involves exposing the polymer material to UV light through the film negative. The areas exposed to light harden, while the unexposed areas remain soft.
Plate mounting
The flexographic printing plate is mounted onto a printing cylinder on the printing press. Precision is crucial during this step to ensure accurate registration of the image during printing.
Color separation
In multi-color printing, each color is separated into different plates using a set of filters to create individual color channels. Each plate represents a specific color, and the combination of these colors during printing reproduces the full-color image.
Dot generation
The process involves creating dots on the flexographic plate to represent different tones and shades. The size and arrangement of these dots determine the final appearance of the printed image.
Proofing
Before the actual printing begins, a physical or digital proof is created to verify the design and colors.
Plate cylinder setup for flexo printing presses
The flexo printing press is set up with the appropriate plate cylinders, inks, and substrate, adjusting the press to achieve proper registration, pressure, and ink transfer.
The pre-press stage is crucial for ensuring that the flexographic printing process accurately reproduces the intended design. Proper plate preparation and setup contribute to the quality and consistency of the final printed product in flexographic printing.
Request a Demo: Packaging Design Software
Our intuitive packaging design software allows your customers to quickly create and preview their custom packaging boxes.
2. Printing stage in flexographic printing:
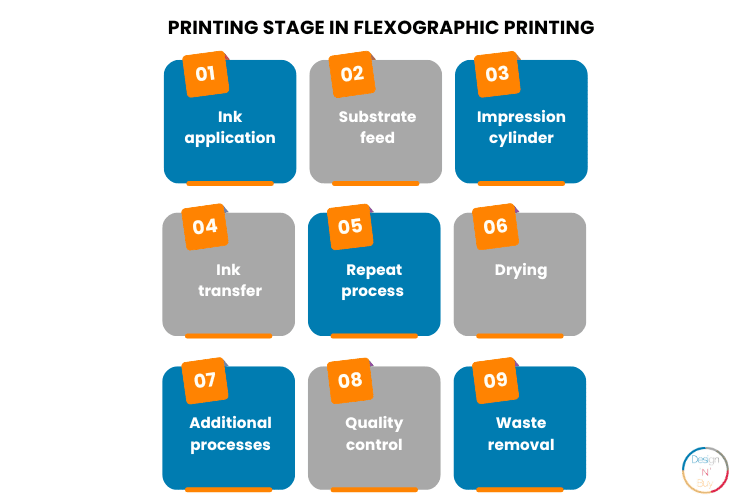
Ink application
The flexographic printing presses are equipped with an inking system that applies ink to the raised portions of the flexible printing plates. The ink is typically a liquid or paste that adheres to the plate’s image areas. Specialty flexographic printing inks with unique properties or effects beyond standard printing inks such as metallic inks, fluorescent inks, and thermochromic inks are also used for the desired results.
Substrate feed
Materials such as paper, plastic, or cardboard serve as the substrate, fed through the flexographic printing press, typically in a continuous roll.
Impression cylinder
As the substrate moves through the flexographic printing press, it comes into contact with the rotating printing plate cylinder. The substrate is pressed against the inked printing plate on the plate cylinder.
Ink transfer
The inked portions of the flexible printing plate transfer the image onto the substrate. The flexible nature of the printing plate allows it to conform to the shape of the substrate, making flexography suitable for printing on various materials.
Repeat process for multiple colors
In multi-color printing, each printing unit on the press applies a different color. The substrate passes through each printing unit successively, and the colors are layered to create the final full-color image.
Drying
After the ink is transferred to the substrate, a drying process follows to set the ink with the help of air dryers, UV lamps, or other drying methods, depending on the ink type and substrate.
Additional processes
Additional processes, like coating, laminating, die-cutting, or other finishing processes, may be included based on the specific requirements of the printed material.
Quality control
Throughout the printing stage, operators monitor and adjust various parameters to ensure print quality including maintaining proper ink density, registration (alignment of different colors), and overall print consistency.
Waste removal
As the printed substrate continues its path through the press, any waste or excess material is typically trimmed or removed, resulting in the final printed product.
Request a Demo: Online Form-based Quick Editor
Customers can effortlessly customize their print orders with easy customization of colors, fonts, images and and other appealing design options.
3. Post-press stage in flexographic printing:
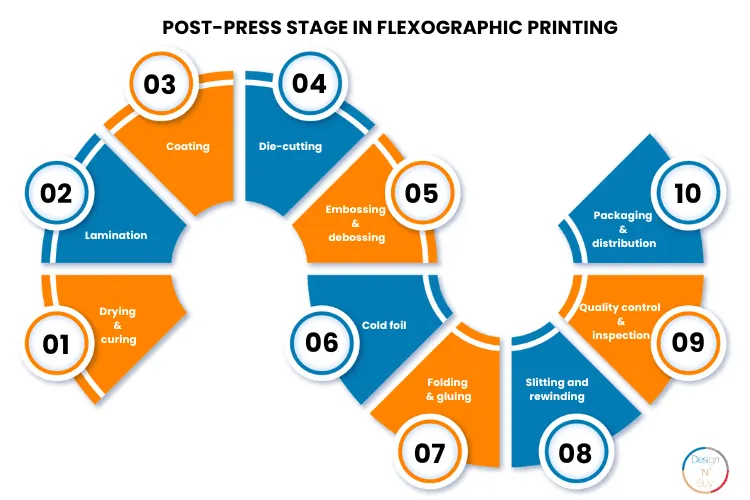
Drying and curing
After the printing stage, the printed material may undergo additional drying or curing processes, especially if UV inks are used. These processes ensure that the ink is fully set and adheres securely to the substrate.
Lamination
After drying, lamination is done for aesthetic or functional purposes by adding a thin layer of transparent film to the printed material to enhance the appearance, provide a glossy or matte finish, and protect against wear and tear.
Coating
Printed materials are coated with UV, aqueous, or other specialty coatings to achieve specific characteristics, such as water resistance, scratch resistance, or additional gloss.
Die-cutting
Next comes the cutting of printed material into specific shapes using a die which is common for labels, packaging, and other materials where a precise shape is required.
Embossing and debossing
Embossing involves creating a raised pattern or design on the printed material while debossing creates a depressed pattern. These techniques add a tactile and visual dimension to the printed product, enhancing its aesthetic appeal.
Cold foil
A process where metallic foil is applied to printed material without requiring heat, resulting in a metallic or reflective effect on specific areas. This method, often utilized for packaging, labels, and promotional materials, offers a cost-effective alternative to traditional hot foil stamping.
Folding and gluing
If the printed material is intended to be folded or assembled into a specific structure (such as a box or packaging), folding and gluing processes are applied.
Slitting and rewinding
Slitting involves cutting the printed material into narrower rolls or sheets, which is especially relevant for large rolls of printed labels or packaging. The rewinding process then prepares the material for packaging and distribution.
Quality control and inspection
Throughout the post-press stage, quality control measures are implemented to check for defects, ensure consistency, and verify that the finished product meets the specified standards.
Packaging and distribution
The final printed and finished products are then packaged and prepared for distribution, including bundling, boxing, or other packaging methods depending on the nature of the printed material.
Ready to Hit 1000% ROI – From Order To Delivery
With DesignNBuy, your journey from order to delivery is seamless, ensuring top-notch
quality every step of the way.
Essentials for Flexographic Printing
To achieve high-quality prints, certain requirements must be fulfilled, as follows:
Flexographic printing press
It goes without saying that for printing, a printing press is necessary, and flexographic printers come in various configurations to cater to different printing needs. The choice of a specific type of flexographic printer depends on factors such as the application, substrate, printing volume, and required features.
Some common types of flexographic printers are Stack Press, Central Impression Press, In-Line Press, Modular Press, Wide-Web Press, Narrow-Web Press, and Digital Flexographic Press that can handle various functions like multiple colors, printing speed, and additional features such as drying systems and inline finishing capabilities.
Flexographic printing plates
Responsible for transferring the image or design onto the substrate during printing, flexographic printing plates are typically made of flexible materials, and the most common is the digital photopolymer plates, made from a light-sensitive polymer material that provides high image quality and resolution.
Then there is also a rubber plate also known as an elastomer plate, made from a rubbery material, and Digital Flexographic Plates created using digital imaging technologies, bypassing the traditional film-based exposure.
Ink systems
Flexographic inks are extremely versatile specially formulated inks designed for use in the flexographic process on a variety of substrates. They are Water-Based Inks made primarily from water, pigments or dyes, and other additives commonly used for paper and cardboard substrates; Solvent-Based Inks, suitable for non-porous substrates like plastic films, metallic surfaces, and synthetic materials; UV Inks that are suitable for various substrates, offering high print quality.
In flexographic packaging, ink color systems are crucial for achieving accurate and vibrant colors on a variety of substrates. Flexo printers commonly use different ink color systems to achieve specific color requirements like:
Process color (CMYK) – a combination of four ink colors: Cyan, Magenta, Yellow, and Key (Black) commonly used for full-color printing to achieve a broad spectrum of colors, including photographs and detailed graphics.
Expanded gamut printing – a blend of additional inks and traditional CMYK color model, commonly used extended gamut systems include CMYK + Orange, Green, and Violet (CMYKOGV).
Spot colors – pre-mixed inks formulated to match specific colors using standardized color-matching systems like Pantone or HKS. Each spot color is a unique ink formulation.
Specialty Inks – inks such as metallic inks or fluorescent inks used for eye-catching designs in labels and packaging.
Anilox rollers
Anilox rollers are responsible for transferring ink from the ink pan to the printing plates and, ultimately, to the substrate. Their varying cell counts determine the amount of ink transferred, thereby affecting print quality.
Substrates
Flexographic printing can accommodate a variety of substrates, each with its own characteristics. Some common substrates used in flexographic printing are – paper, plastic, metalized films, cardboard and cardstock, flexible packaging materials, corrugated board, textiles, foam board, labels, synthetic papers, and so on.
Drying systems
The curing or drying of inks on the printed substrate in flexographic printing is carried out through drying systems like Hot Air Dryers, Infrared (IR) Dryers, UV (Ultraviolet) Dryers, LED UV Dryers, or EB (Electron Beam) Dryers.
Color management systems
CMS in flexographic printing ensures consistent and accurate color reproduction across various devices and print runs. These systems help maintain color integrity from the initial design stage to the final printed product. It involves the use of various components like color spaces, ICC profiles, color measurement tools, color matching software, and spectrophotometer.
Pre-press software
It encompasses a range of applications and tools that are used in the preparation and optimization of digital files before they are sent to the printing press. Some key types of pre-press software commonly used in flexographic printing are Graphic Design Software, Pre-Press Workflow Software, Color Management Software, RIP Software (Raster Image Processor), Variable Data Printing (VDP) Software, etc.
It is a web to print software solution that allows users to order, customize, and print marketing materials, promotional products, and other print-related items through a web interface. It streamlines the printing process by providing an online platform where customers can design, proof, and submit print orders in your web to print store.
Its features include – Online Design Tools, Template Management, Order Management, Variable Data Printing (VDP), File Upload and Proofing, Integration with Printers and Production Systems, Multi-Channel Support, Responsive Design, Security and Permissions, and so on.
CRM software
Customer Relationship Management (CRM) software helps businesses manage and analyze interactions with their current and potential customers. It streamlines processes, improves customer engagement, and enhances overall business efficiency.
Quality control tools
It is necessary to monitor and ensure the consistency and excellence of products or services for which certain tools are utilized that help identify and rectify defects, errors, or deviations from established quality standards. Some common, widely used quality control tools are – Flowcharts, Fishbone Diagram, Histograms, Scatter Diagrams, Statistical Sampling, Six Sigma Tools (DMAIC), etc.
ERP systems
Enterprise Resource Planning (ERP) systems are integrated software solutions that organizations use to manage and streamline their business processes and functions across various departments. ERP systems provide a centralized database and a unified platform for real-time collaboration, enabling efficient data sharing and decision-making.
Finishing equipment
Machinery and tools used in the final stages of the printing process to add special effects, refine the appearance, and prepare printed materials for distribution are finishing equipment. Some common types of finishing equipment used in flexoprinting are – Cutting and Trimming Equipment, Folding Machines, Binding Machines, Laminators, Die-Cutting Machines, Embossing and Debossing Machines, UV Coating Machines, Foiling Machines, Perforating Machines, Collating Machines, etc.
These essentials contribute to a well-equipped flexographic printing setup, ensuring efficiency, quality, and the ability to meet diverse flexographic printing companies’ requirements. The choice of equipment and materials depends on the specific needs of the printing operation and the types of products being produced.
List of Fexographic Printing Products
Being versatile flexographic printing process finds applications in various industries. Here is a list of common products and applications of the flexographic printing process are:
- Flexible Packaging
- Labels
- Wallpaper
- Textiles
- Foil Printing
- Food and Beverage Packaging
- Folding Carton
- Envelopes
- Brown Corrugated Boxes
- Medical and Pharmaceutical Packaging
- Newspaper and Print Media
- Consumer Products
- Non-Rigid Materials
- Self-Adhesive Labels
- Home, School, and Office Products
- Marketing Materials
- Product Packaging
Flexographic printing’s ability to print on different substrates, including flexible materials, makes it suitable for a diverse range of applications.
Flexographic Printing Advantages
Flexographic printing offers several advantages, making it a popular choice for various printing applications. Here are some key advantages of flexographic printing:
- Suitable for diverse substrates, including paper, plastic, and metallic films.
- Economical for high-volume runs with low setup costs.
- Ideal for large print runs with efficient production.
- Modern technology ensures sharp images and consistent colors.
- Supports vibrant and customized color choices for branding.
- Uses eco-friendly water-based and UV-curable inks.
- Allows for laminating, die-cutting, and varnishing in the same process.
- Prints on diverse materials for packaging applications.
- Resistant to abrasion, suitable for labels and packaging.
- Well-suited for wide-format materials like banners and large packaging.
- Handles varying substrate thicknesses, providing flexibility.
- Enables efficient transitions between print jobs.
While flexographic printing has many advantages, the choice of a flexographic printing machine and method depends on specific requirements, including print quality, substrate, and production volume. Advances in technology continue to enhance the capabilities and competitiveness of flexo printing in the modern printing industry.
Flexographic Printing Disadvantages
While flexo printing offers many advantages, it also has some limitations and disadvantages. It’s important to consider these factors when choosing a printing method. Here are some of the disadvantages associated with flexographic printing:
- Involves upfront costs and lead times for plate-making, contributing to initial expenses.
- Achieving precise color matching can be more challenging in flexography compared to other printing methods.
- Flexographic inks may emit odors, and solvent evaporation during drying can be a concern, especially in sensitive environments like food packaging.
- Flexographic inks require drying time, potentially slowing down production, especially on certain substrates.
- Regular maintenance and involved cleanup processes can extend the overall production time.
- Flexographic plates can wear over time, requiring replacement for consistent print quality.
- It is less suited for variable data printing compared to digital methods.
- Flexographic presses can be noisy during operation, which may impact certain production environments.
While these disadvantages exist, it’s important to note that flexographic printing remains a widely used and cost-effective method for many applications, particularly in the packaging industry. Advances in technology and ongoing improvements in flexographic processes continue to address some of these limitations. The choice of a flexographic printing solution or method should be based on the specific requirements and priorities of the printing project.
Automate Your Workflows, Empower Your Customers 🚀
Our user-friendly platform allows customers to personalize stationery items with ease, fostering higher customer satisfaction and loyalty.
In Conclusion
Flexo printing is a winner. It deserves the top position it is today in the print market because of the set of advantages and unique features it offers. Nothing can match its versatility, speed, print quality, and automation which is what every printing professional desires.
We hope our guide has covered all the intricacies of flexographic printing, if you need to know further, stay tuned we will keep updating you on the latest and future trends about flexo printing for you.
*This Post has been Updated on January 2025.